Selecting the Best Pharmaceutical Quality Management Software for Your Needs
- QualityPro by TecWork
- Nov 11, 2024
- 3 min read
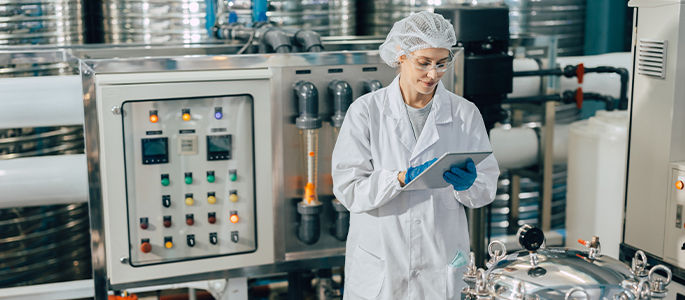
Imagine you're in a shoe store with countless options. Some pairs catch your eye with their stylish design, but they pinch your toes and are uncomfortable. Others feel like walking on clouds but lack the style you desire. You might also face budget constraints, with some shoes fitting your price range and others being too expensive. Eventually, you find the perfect pair—stylish, comfortable, and reasonably priced. As soon as you try them on, you know they're just right, offering the support you need without exceeding your budget. You feel satisfied and finally make the purchase.
Selecting the best Pharmaceutical Quality Management Software (QMS) is somewhat similar to finding the right pair of shoes. With so many QMS software available in the marketplace, it’s important to select the one that not only fits your business needs but also helps eliminate challenges, supports growth, and is affordable. Just like your shoes, your QMS should be easy to operate while providing the functionality and reliability your business requires.
In the pharmaceutical sector, where precision, compliance, and efficiency are crucial, choosing the right manufacturing quality management system is not just a formality; it's a critical investment. The solution should align with your company's specific needs and budget, going beyond what's on paper. You should focus on finding a QMS that effectively digitizes quality across workflows and processes, ensuring it supports operational goals without excessive costs.
So, how do you ensure you’re making the right choice? Following are the key factors to consider when selecting the ideal QMS for pharma operations:
Identify Your Specific Requirements When selecting a QMS system, it's crucial for top-level employees to clearly define their business's unique challenges and needs. This involves pinpointing key issues such as document management inefficiencies, gaps in risk identification, inadequate audit trails, and the lack of effective CAPA (Corrective and Preventive Action) processes.
Research and Evaluate Vendors Look for pharma QMS vendors with a strong industry track record and ensure their solutions align with your specific needs. Review customer feedback, request demos, and use trial periods to assess compatibility and ease of use. This approach helps you make an informed choice for your business.
Seek Comprehensive Functionalities Ensure the QMS vendor offers essential features like document control, audit management, CAPA, risk management, training management, and reporting tools to meet all your quality management needs.
Check Integration Capabilities Ask the vendor about how the QMS will integrate with existing systems like ERP or CRM to ensure seamless data flow.
Evaluate Usability Opt for software with an intuitive interface and easy navigation to minimize the learning curve and enhance efficiency.
Prioritize Compliance and Security Select a QMS that helps document and meet global regulatory standards and offers robust security features, such as data encryption, access controls, and authorizations.
Consider Customization and Scalability Confirm that the QMS can be tailored to your current business processes and check its scalability to accommodate future growth.
Assess Cost-Effectiveness Evaluate the total cost of ownership, including initial costs, implementation, and ongoing maintenance, to ensure good value for your investment.
Gather Feedback from Users Involve your team in the selection process to collect their feedback on functionality and usability, ensuring successful adoption. One such QMS for pharma industry that meets these criteria is QualityMaster by TecWork. As a leading solution for pharmaceutical manufacturers, QualityMaster excels in developing risk-based CAPA processes, managing non-compliance through comprehensive QMS documentation, ensuring employee adherence to processes, and completing audit checklists. It equips organizations with the tools needed to maintain quality throughout the product lifecycle till post-market support.
With its extensive features, customizable solutions, and strong industry reputation, it effectively addresses your pharmaceutical quality management needs, ensuring compliance, efficiency, and growth.
Comentarios